Building a Mother-in-law House
- Matt Weber
- May 11, 2021
- 4 min read
(guest post courtesy of Will Chelak)

A perfect blend of nature and commerce, Beaverton, Oregon sits just seven miles outside of Portland to combine the natural beauty of the area’s parks, vineyards, forests and trails with the world headquarters of leading corporations like Nike, Inc.
Bill Campbell truly understood these benefits when he built his first house in the Brook Haven section of West Beaverton more than 30 years ago. Armed with little more than a “background in construction as a young man” and a class on “Building Your Own House” at the local community college, Campbell spent the better part of 18 months on the design and build of a 2,600 sq. ft, three-bedroom house that would be the family’s home for more than three decades.
“It was really exhilarating doing the whole thing from the ground up yourself,” says Campbell. “There’s a real sense of achievement that accompanies the effort. Plus, the location couldn’t have been better We’re situated on the edge of the wetlands and up against a creek in the park district. It’s like having a wildlife park in your own backyard.”
Despite the view and the thought of leaving the area they’d come to love, Campbell was approaching retirement and looking to downsize. So, his family devised the perfect plan. Their daughter would move into the main house after Bill Campbell finished the design and build of an 800 sq. ft. mother-in-law home situated next to his existing house on the same property.
The only problem was that the township’s building code mandated that the aesthetics of both homes had to mirror each other. The new house literally had to be “mini-me” of the older structure.
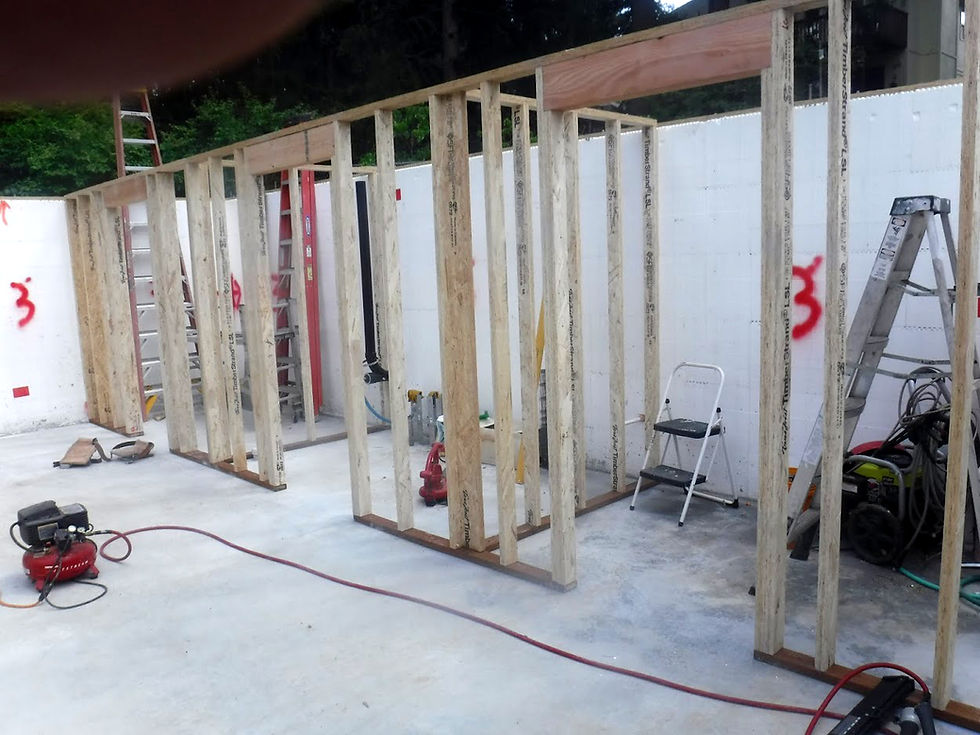
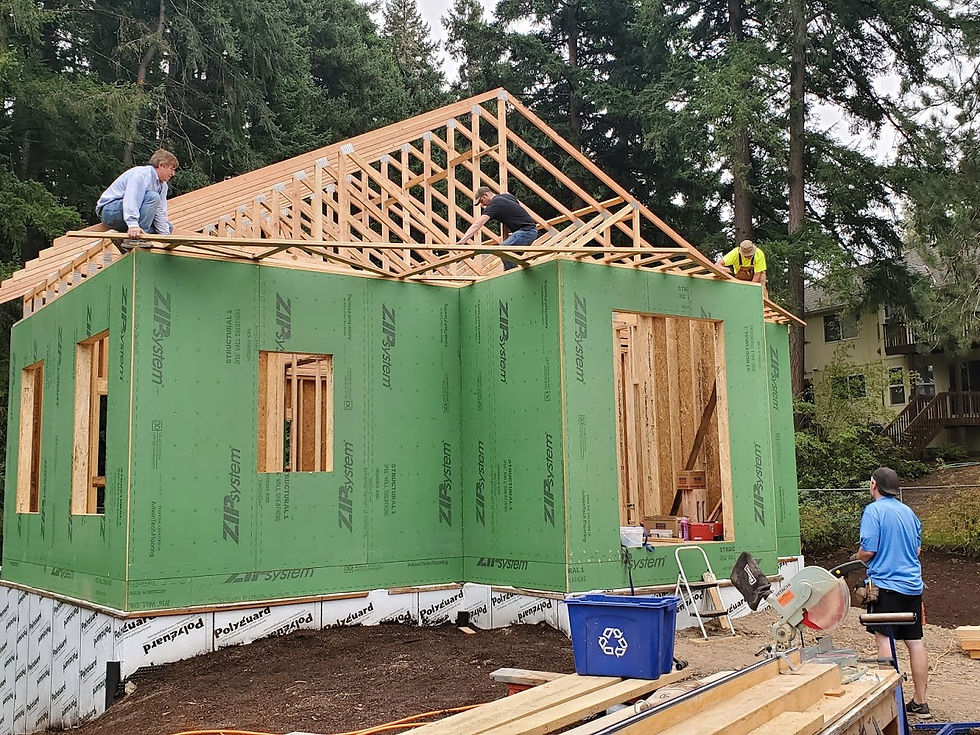

Knowing this would be his last major project, Campbell set out to build not only the smaller home, but upgrade the larger one with the same, long-lasting materials. For Campbell, this meant combining everything he learned from the first experience with the latest in building science.
“Everything was designed with an emphasis on longevity and low maintenance,” offers Campbell. “Ideally, all the materials used would last for the next 30 years. As a result, we started to look at rainscreen ideas and the implementation of exterior control layers that would ensure both homes would stay water- and air-tight even during the wet, cold winters that are common throughout the Portland area."
Rainscreen System for Exterior Protection
In addition to the specification of natural, stone-cut veneers for the bases and installation of steel metal roofing, Campbell decided on Batu Rainscreen Siding from Nova USA Wood Products for the exterior of both homes after carefully researching various alternatives. Around for centuries, a rainscreen system entails fastening the siding to the structure with an air gap left between the siding material and the structure itself. Normally about 3/4-inches, the gap is specifically designed to create an air cavity that protects the exterior walls of the building from debris, rain and other elements, while also reducing the possibility of water filtration and leakage.
The siding was then secured by Nova USA Wood’s ExoClad Rainscreen QuickClips, which accommodates the natural swelling and shrinkage of wood siding throughout all the seasons. This includes expanding when the wood swells and compressing back into its original form when the wood dries out and/or shrinks to prevent the siding from buckling or the clip from breaking.


Another benefit was the beauty of the Batu or Red Balau hardwood siding itself, which closely resembles the rich classic look of Mahogany. This includes a moderately-fine texture and interlocking grain that ranges from a medium red to a deep red/brown with purple tinges to produce warm, visually striking effects.
“Everything on the 30-year-old house’s exterior was replaced but the doorbell,” explains Campbell. “We then used the same material on the second home to ensure they both had the same look and feel.
“Thanks to the QuickClips the install of the Batu siding was probably one of the easiest parts of the whole process. Once the clips are secured in a straight line, all you have to do is layer one course of siding on top of the other. With a little help, it took me about two weeks total to finish the siding on each house.”
Once the work on both homes was complete, the Campbell family turned their attention to the rebuild of the 30-year-old, 600 sq. ft. deck at the main house as well as the design and build of a hardwood front porch, walkway and L-shaped deck at the mother-in-law home. To achieve this task, Campbell chose Nova USA Wood’s rich honey- and reddish-brown Cumaru decking. This is not only because of the hardwood’s exotic, warm tones, but also its strength, stability, durability and natural resistance to decay, wet conditions, termites and wood-boring insects.
“The deck and remaining woodwork at the mother-in-law house were built in a matter of days with the aid of Nova USA Wood’s ExoDek® QuickClip ™ hidden deck fastener system,” says Campbell. “All you have to do is follow the directions and make sure each board is snug against the previous one. My wife and I did all the work ourselves. I drilled down the screws immediately after she put the clips in place. It was a breeze.”
After two years of work, Campbell celebrated the completion of his second home on Memorial Day 2021. “Our new house provides an elevated view of the creek that is absolutely stunning,” adds Campbell. “We’re thrilled with the way everything came out. Everyone speaks about curb appeal. For us, curb appeal is coming home every day to a beautiful home we built ourselves.”

# # # #
Launched in 2005, Nova USA Wood Products is dedicated to the supply of superior, high-quality hardwood products and. For more information, visit www.novausawood.com or call 503-419-6407.
Background and people search services have become essential tools for employers, landlords, and even individuals seeking safety and transparency. Among these services, Checkr stands out for its modern approach to background checks, using technology to streamline screening processes. It supports hiring teams by providing fast access to employment history, criminal records, and more. Whether you're vetting a new tenant or verifying someone’s professional background, platforms like Checkr help ensure you're working with accurate and timely information, without unnecessary delays or complications.